I część artykułu (zamieszczona w poprzednim numerze „Buduj z Głową”) zawierała przegląd posadzek przemysłowych ze względu na rodzaj wymagań im stawianych i sposób wykonania. Przedstawiłem w niej schematy różnych rozwiązań i w skrócie omówiłem ich zalety.
Warstwy użytkowe posadzki są odpowiedzialne nie tylko za ochronę przed czynnikami chemicznymi i obciążeniami mechanicznymi, dodatkowo w przypadku posadzek w pomieszczeniach mokrych konieczne jest uzyskanie odpowiedniej klasy antypoślizgowości. Antypoślizgowość definiowana jest strukturą wierzchniej warstwy, przy której (przy nachyleniu pod odpowiednim kątem) noga w typowym obuwiu roboczym nie poślizgnie się. Klasy antypoślizgowości oznacza się symbolami od R9 do R13. Dodatkowym parametrem, istotnym dla posadzek w pomieszczeniach mokrych, jest zdolność do gromadzenia zanieczyszczeń, zarówno ciekłych jak i stałych, w sposób nie powodujący niebezpieczeństwa poślizgu. Jest to realizowane poprzez uzyskanie wolnej przestrzeni pomiędzy najniższym a najwyższym punktem warstwy użytkowej posadzki. Rozróżnia się cztery klasy tzw. przestrzeni wypełnienia (zaznaczono ją strzałką na rysunku 1): V4, V6, V8 i V10 (liczba mówi o objętości dostępnej przestrzeni w cm3 na 1dm2 powierzchni posadzki).
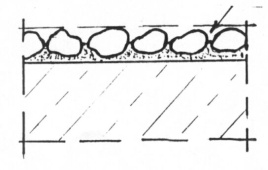 |
Rysunek 1 Posadzki przemysłowe – przestrzeń wypełnienia
|
W tablicy 1 podaję przykładowe wymagania w zakresie antypoślizgowości posadzek w zakładach przetwórstwa żywności, kuchniach i warsztatach naprawczych. Pełen wykaz znaleźć można w niemieckich wytycznych: „Fußböden in Arbeitsräumen und Arbeitsbereichen mit erhöhter Rutschgefahr ZH 1/571, IV.1989
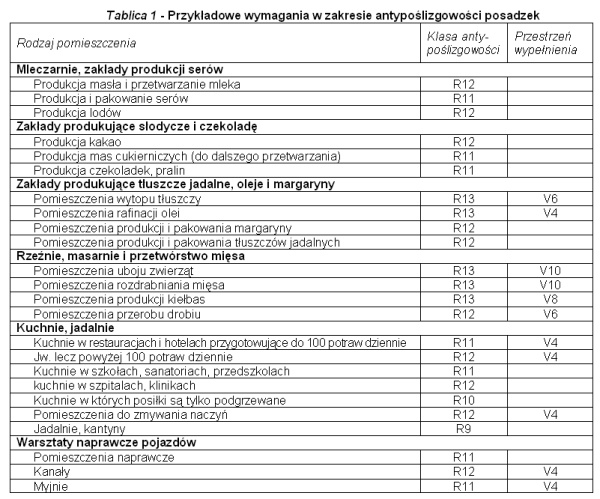
Jak wcześniej wspominałem, już warstwa betonu podkładowego (nie - chudego betonu) musi być zabezpieczona przed podsiąkaniem kapilarnym. Często zapomina się, że warstwa ubitego piasku nie przerywa podciągania kapilarnego wilgoci. Uzyskać to można np. przez stosowanie warstwy żwiru płukanego o uziarnieniu 8÷16mm (grubość warstwy 20÷40 cm) lub specjalnych membran kubełkowych. Natomiast na warstwie betonu podkładowego wykonać należy hydroizolację posadzki. Stosuje się tu materiały typu:
– papy termozgrzewalne,
– bitumiczne membrany samoprzylepne,
– szlamy uszczelniające czy
– bitumiczne masy typu KMB.
Na warstwę termoizolacji, jeżeli jest wymagana, należy stosować materiał o odpowiednio niskiej odkształcalności i wysokiej wytrzymałości, np. polistyren ekstrudowany.
Uwaga: materiały bitumiczne stosowane do izolacji na betonie podkładowym nie mogą zawierać rozpuszczalników.
Jako warstwę ochronną, przy braku obciążeń chemicznych, stosować można zwykłą folię PE; w przeciwnym przypadku konieczne jest użycie np. specjalnych, zgrzewanych na złączach folii PCW lub membran cechujących się dodatkowo chemoodpornością.
Pierwszą „linią oporu” przed obciążeniem chemicznym i mechanicznym jest warstwa użytkowa. Odpowiednie przygotowanie podłoża jest podstawowym warunkiem poprawnej aplikacji.
Powierzchnia betonu musi być czysta oraz wolna od substancji mogących pogorszyć przyczepność (luźne i niezwiązane cząstki, środki antyadhezyjne, zabrudzenia itp.). W zależności od rodzaju oraz intensywności zabrudzenia konieczne jest stosowanie odpowiednich środków zaradczych (odkurzanie, czyszczenie mechaniczne, zmywanie, szorowanie, szlifowanie, piaskowanie, frezowanie, śrutowanie itp.).
Jedyną skuteczną metodą usunięcia zanieczyszczeń olejowych jest usunięcie skażonego podłoża. Inne metody, tj. stosowanie specjalnych preparatów czyszczących oraz mechaniczne zmycie czy szorowanie itp. nie dają stuprocentowej gwarancji usunięcia skażeń z podłoża.
Alternatywą dla usuwania skażonego podłoża jest stosowanie systemowych gruntowników na zaolejone podłoża.
Technologię oczyszczania podłoża podaje zawsze producent systemu. Polega ona generalnie na mechanicznym oczyszczeniu i zmyciu podłoża, następnie na rozprowadzeniu na podłożu preparatu czyszczącego, starannym wtarciu go w podłoże oraz mechanicznym odessaniu zanieczyszczeń z podłoża. Kolejnym etapem jest naniesienie na podłoże (natychmiast po odessaniu zanieczyszczeń) systemowego gruntownika oraz ewentualne wykonanie posypki z piasku kwarcowego o ściśle określonym uziarnieniu.
Oczyszczanie podłoża
Zalecaną metodą usunięcia zanieczyszczeń materiałami bitumicznymi, farbami oraz smołami jest frezowanie, piaskowanie lub groszkowanie.
Zanieczyszczenia chemiczne można usuwać przez oczyszczanie płomieniowe.
Frezowanie pozwala na usunięcie wierzchniej warstwy podłoża o zbyt niskich parametrach wytrzymałościowych lub zanieczyszczonej trudno usuwalnymi substancjami.
Śrutowanie pozwala na bezpyłowe usunięcie stwardniałego zaczynu cementowego.
Metody hydrodynamiczne - lanca wodna przy ciśnieniu > 80 bar stosowana jest w celu usunięcia zmurszałych i niestabilnych fragmentów podłoża oraz zanieczyszczeń. Ciśnienie > 800 bar pozwala na usuwanie skorodowanych niestabilnych warstw podłoża o większej grubości.
Raki, wykruszenia i inne ubytki, w zależności od ich wielkości, należy uzupełnić zaprawami reprofilacyjnymi (np. typu PCC) lub innymi zaprawami mogącymi służyć do reprofilacji (np. zaprawa cementowo-epoksydowa), jak również szpachlami i zaprawami epoksydowymi.
Wykonanie warstwy użytkowej podłogi
Pierwszą czynnością jest zagruntowanie podłoża systemowym gruntownikiem i wykonanie posypki z piasku kwarcowego. Po związaniu gruntu (zwykle jest to okres 12÷16 godzin) nadmiar piasku należy usunąć i nanieść żywicę będącą warstwą użytkową podłogi. Można to zrobić ręcznie: za pomocą wałka, pędzla, szpachli lub mechanicznie za pomocą agregatu natryskowego, zgodnie z wytycznymi producenta. Powłoki nanoszone wałkiem należy rozprowadzić równomiernie na podłożu np. za pomocą specjalnej listwy a następnie przy pomocy wałka z krótkim włosiem (jest to specjalny wałek do żywic!) energicznymi ruchami w prostopadłych do siebie kierunkach wetrzeć w podłoże. Materiał wylewany rozprowadzić równomiernie za pomocą kielni lub rakli warstwą o odpowiedniej grubości, a następnie odpowietrzyć wałkiem z kolcami. Jeżeli jest to wymagane, wykonać posypkę z piasku kwarcowego o uziarnieniu podanym przez producenta systemu. Po związaniu żywicy, nadmiar piasku usunąć i nanieść drugą warstwę żywicy.
Wymaganą antypoślizgowość nadaje się wykonując na świeżo ułożonej warstwie żywicy posypkę z piasku kwarcowego lub korundu; po związaniu, nadmiar piasku należy usunąć i wykonać lakierowanie powierzchni (patrz tablica 2).
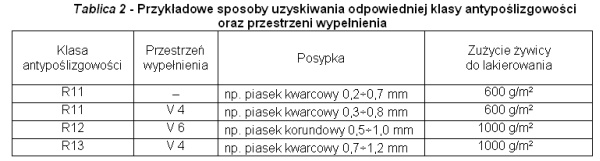
Dylatacje
Nie mniej ważnym elementem konstrukcji podłogi są dylatacje (patrz rysunki nr 2 i 3), połączenia posadzki ze ścianą (patrz rysunki nr 4 i 5), czy np. odwodnienia, zarówno liniowe jak i punktowe.
Rysunek 2
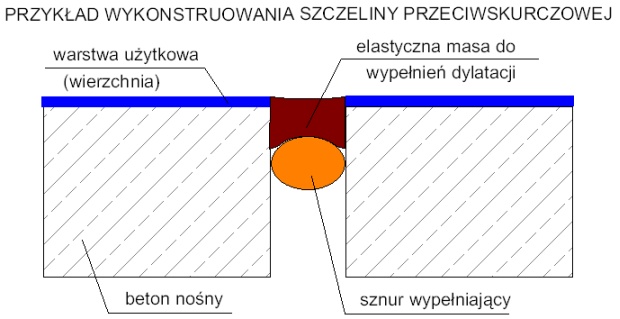
Rysunek 3
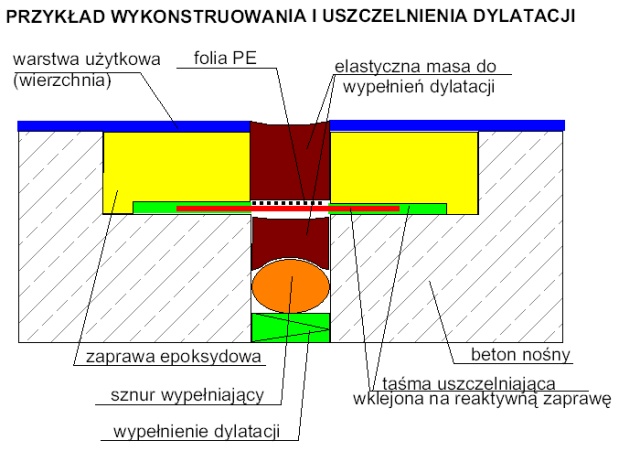
Prawidłowe zaprojektowanie dylatacji, jej umiejscowienie, wyprofilowanie oraz dobór materiału do wypełnienia (zazwyczaj stosuje się masy poliuretanowe, poliuretanowo-epoksydowe i tiokolowe), dodać trzeba - odpornego na projektowane obciążenia mechaniczne, chemiczne i termiczne, decyduje w dużym stopniu o jakości i trwałości posadzki.
Cokoliki
Odpowiednio zaprojektowany musi być ponadto sposób połączenia posadzki ze ścianą (cokolik). Chodzi tu o jego wymiary, ewentualny sposób uszczelnienia itp.
Rysunek 4
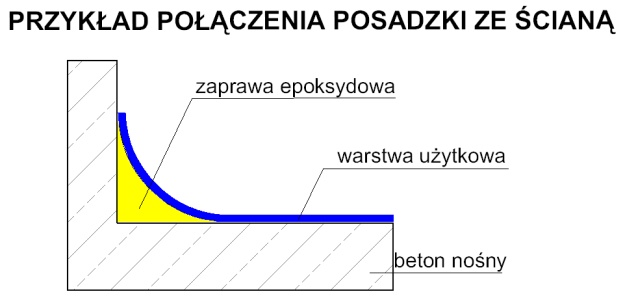
Rysunek 5
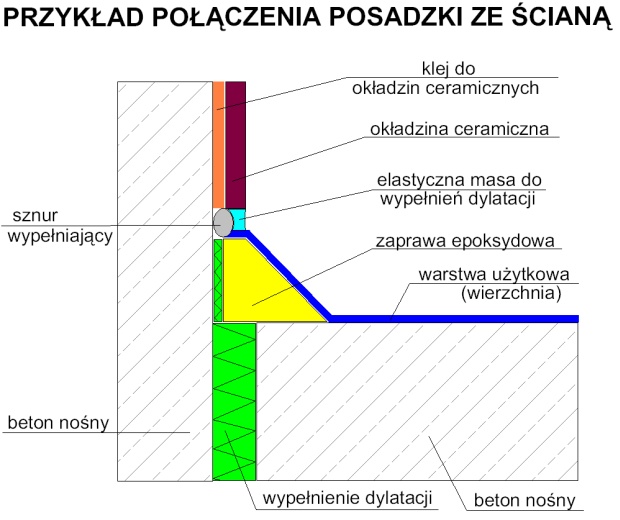
Wpusty
Przy projektowaniu i wykonywaniu wpustów należy zwrócić uwagę nie tylko na spadki, lecz - co istotne w przypadku dużych obciążeń mechanicznych, także na sposób zabezpieczenia przed mechanicznym uszkodzeniem.