Ze względu na okładziny ceramiczne podłoża gipsowe podzielić można na 3 rodzaje:
- jastrychy anhydrytowe,
- płyty gipsowo-kartonowe (gk),
- tynki gipsowe - wykonywane zarówno maszynowo jak i ręcznie.
Jastrychy anhydrytowe
Mogą być stosowane wyłącznie wewnątrz i tylko w suchych pomieszczeniach. Jedynym dopuszczalnym wyjątkiem to pomieszczenia I klasy obciążenia wilgocią wg wytycznych ZDB „Hinweise für die Ausführung von Abdichtungen im Verbund mit Bekleidungen und Belägen aus Fliesen und Platten für den Innen- und Aussenbereich” – będzie to krótkotrwałe obciążenie wilgocią rozbryzgową (np. natrysk) - zaliczyć tu można łazienki i pomieszczenia sanitarne z wannami lub brodzikami, w których woda odprowadzana jest bezpośrednio do kanalizacji. W takiej sytuacji niezbędne jest wykonanie hydroizolacji bezpośrednio pod okładziną ceramiczną – tzw. uszczelnienie zespolone (patrz rysunek). Podstawowym jednak zastosowaniem jastrychów anhydrytowych jest budownictwo mieszkaniowe i użyteczności publicznej.
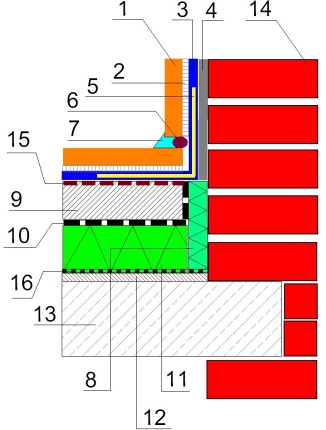 |
Szczegół izolacji styku podłogi ze ścianą I klasa obciążenia wilgocią wg ZDB - jastrych anhydrytowy
- okładzina ceramiczna
- klej typu „flex”
- hydroizolacja (folia w płynie, elastyczna zaprawa uszczelniająca)
- tynk tradycyjny
- taśma uszczelniająca
- sznur wypełniający
- silikon sanitarny z systemowym gruntownikiem
- dylatacja obwodowa
- jastrych anhydrytowy samopoziomujący
- folia PE
- płyty izolacji termiczno-akustycznej
- warstwa niwelująco-wygładzająca
- strop
- ściana
- preparat gruntujący do podłoży gipsowych
- paroizolacja
|
Powierzchnię jastrychu anhydrytowego, przed ułożeniem okładziny ceramicznej należy ocenić pod względem występowania ewentualnych wad oraz wymaganej równości. Niezbędne jest także mechaniczne przeszlifowanie powierzchni papierem ściernym w jednym przejściu, oraz bardzo staranne odkurzenie jej odkurzaczem przemysłowym.
Obecność luźnych i niezwiązanych cząstek wykryć można np. przez przetarcie podłoża ręką. Po przeszlifowaniu, a przed wykonaniem okładziny ceramicznej, podłoże należy zagruntować. Używać należy preparatów, które mogą być stosowane na podłoża zawierające gips oraz kompatybilnych z zastosowaną zaprawą klejową lub materiałem uszczelniającym, jeżeli wykonywane jest uszczelnienie podpłytkowe. Należy tu przestrzegać wytycznych producenta (chodzi zwłaszcza o przygotowanie podłoża, jak również sposób aplikacji gruntownika – np. konieczność rozcieńczania, oraz o przestrzeganie minimalnych czasów schnięcia).
Podczas schnięcia jastrychu, na jego powierzchni może tworzyć się cienka warstwa zawierająca rozpuszczone w wodzie zarobowej dodatki oraz spoiwo. Powstaje ona zazwyczaj w pierwszych dniach po ułożeniu i ma grubość rzędu ułamków milimetra, może być zarówno matowa jak i błyszcząca. Obecność takiej warstewki można stwierdzić w większości przypadków wizualnie lub wykonując siatkę nacięć w odstępach 10-milimetrowych. Jeżeli na powierzchni jastrychu utworzyła się warstewka związanego spoiwa, ulega ona podczas tej próby skruszeniu. W sytuacjach wątpliwych wykorzystać można aparat „pull off”. Można ją usunąć np. przez przeszlifowanie podłoża.
Na skutek nadmiernej miejscowej koncentracji spoiwa i dodatków mogą tworzyć się lokalne, bardzo twarde warstwy/miejsca, utrudniające wysychanie głębiej położonego materiału. Pod obciążeniem mają one tendencję do odspajania się od głębiej położonych warstw. Można je wykryć przy pomocy np. młotka ślusarskiego o wadze około 500 g. Młotek należy ustawić pod kątem 45o÷60o i swobodnie puścić. Usunąć takie miejsca można ręcznie lub mechanicznie (np. przez sfrezowanie lub zeszlifowanie).
Białe, miękkie pola powstają na powierzchni jastrychu zarobionego zbyt dużą ilością wody. Zawierają one spoiwo oraz dodatki, cechują się grubością nawet rzędu milimetra, występują zawsze na powierzchni jastrychu i ich wytrzymałość mechaniczna jest znacznie niższa od wytrzymałości wylewki. Konieczne jest mechaniczne usunięcie takiej warstwy do uzyskania stabilnego podłoża.
Układane wierzchnie warstwy (okładziny ceramiczne, masy hydroizolacyjne itp.) wymagają odpowiednio i równomiernie chłonnego podłoża. Sprawdzić to można poprzez wykonanie tzw. próby zwilżalności. Polega ona na rozlaniu na powierzchni jastrychu ok. 2 ml wody i pomiarze czasu jej wsiąkania w podłoże. Czas całkowitego wchłonięcia dłuższy niż 3 minuty (lub brak wsiąkania) wskazuje na zbyt małą chłonność podłoża (może także świadczyć o występowaniu stwardniałych pól na powierzchni jastrychu). Badanie to powinno być analizowane łącznie z innymi badaniami. Przyczyną zbyt niskiej chłonności jest zazwyczaj zbyt zwarta wierzchnia warstwa podłoża, środkiem zaradczym jest uszorstnienie powierzchni.
Znacznie większe problemy może powodować zanieczyszczenie powierzchni, zwłaszcza tłuszczami i olejami. Nie zawsze wystarczające może być późniejsze staranne oczyszczenie czy przeszlifowanie i odkurzenie powierzchni. Czasami jedynym rozwiązaniem jest usunięcie zanieczyszczonego fragmentu podłoża.
Cenne informacje można uzyskać wykonując próbne przyklejenie płytki ceramicznej. Na suchym, oczyszczonym i zagruntowanym systemowym gruntownikiem (tzn. nadającym się do stosowania na podłożach anhydrytowych i odpowiednim do rodzaju zastosowanego kleju) jastrychu przykleja się płytkę okładzinową, i po stwardnieniu kleju (zwykle jest to okres kilku dni) odrywa się płytkę od podłoża. Siła niezbędna do oderwania płytki pozwala ocenić nośność podłoża. Podobne informacje można uzyskać poprzez określenie rodzaju zerwania przyczepności (oderwanie od płytki lub w warstwie kleju, oderwanie na styku klej-podłoże, czy też przełom w podłożu).
Bardzo istotnym parametrem jest wilgotność jastrychu anhydrytowego w momencie wykonywania okładziny ceramicznej. Wynosi ona:
0,3 % dla jastrychów z ogrzewaniem podłogowym,
0,5 % dla pozostałych przypadków.
Pomiar wilgotności musi być przeprowadzony aparatem CM. Dopuszczalne jest wykonywanie okładzin ceramicznych przy innych parametrach wilgotnościowych, o ile zezwala na to producent klejów do płytek (jest to jednak wilgotność na poziomie 1÷1,5 %, także określana aparatem CM).
Tynki gipsowe i płyty gk
Płyty gk stosowane pod okładziny ceramiczne muszą przede wszystkim być stabilnie zamocowane. Wszelkiego rodzaju przejścia rur instalacyjnych przez płyty gk muszą być bezwzględnie wypełnione odporną na wilgoć i trwale elastyczną masą uszczelniającą.
Tynki maszynowe, wg zaleceń niemieckich, powinny mieć grubość nie mniejszą niż 1 cm, i na powierzchniach przeznaczonych do obłożenia ceramiką należy je zaciągać w miarę możliwości pionowo, a wyrównując ewentualne nierówności należy je lekko filcować, używając możliwie najmniejszej ilości wody. Powierzchnię należy ocenić wzrokowo. Musi ona ponadto mieć odpowiednią wytrzymałość i chłonność. Ewentualnymi środkami zaradczymi będzie przeszlifowanie powierzchni; w skrajnych przypadkach - usunięcie luźnych i niestabilnych warstw.
Przed rozpoczęciem prac okładzinowych tynk gipsowy musi być suchy w całym swym przekroju; maksymalna wilgotność nie może przekraczać 2%. Jednocześnie jego powierzchnia musi być stabilna i czysta. Gruntowanie powierzchni należy przeprowadzić preparatami przeznaczonymi do podłoży gipsowych (w porównaniu do gruntowników do podłoży cementowych cechują się one zwykle mniejszym rozmiarem cząstek dyspersji wodnej oraz wyższym udziałem tzw. cząstek stałych w dyspersji; preparaty tego typu cechują się też zazwyczaj większą głębokością penetracji w podłoże). Nakładać je trzeba zawsze zgodnie z wytycznymi producenta, w sposób zapewniający ich równomierne wchłanianie przez podłoże. Nie można jednakże dopuścić, aby utworzyły na gruntowanej powierzchni tzw. film, co jest objawem „przegruntowania” podłoża. Efekt „filmu” może spowodować próba gruntowania koncentratem lub preparatem zbyt mało rozcieńczonym wodą w stosunku do wytycznych z karty technicznej. Gruntowanie zmniejsza oraz ujednolica chłonność podłoża, a w pewnym stopniu wzmacnia je powierzchniowo.
Klejenie okładziny ceramicznej lub nakładanie masy uszczelniającej można rozpocząć po całkowitym wyschnięciu gruntu. Najczęściej stosowane są kleje cementowe cienkowarstwowe lub dyspersyjne kleje jednoskładnikowe. Te ostatnie, w porównaniu do cementowych, są bardziej elastyczne. Zaprawy fugujące powinny cechować się jak najmniejszym skurczem przy wiązaniu oraz właściwościami hydrofobowymi.
Literatura:
- M. Rokiel: „Hydroizolacje w budownictwie. Wybrane zagadnienia w praktyce”, Dom Wydawniczy Medium 2006
- Merkblatt 1: Fliessestriche auf Calciumsulfatbasis in Feuchträumen.“ [IGE/WTM, VI.2000]
- Merkblatt 2: „Austrocknung von Fliessestrichen auf Calciumsulfatbasis.“ [IGE/WTM/BDM, VI.2000]
- Merkblatt 3: „Calciumsulfat-Fliessestriche auf Fussbodenheizung“ [IGE/WTM/BDM, VI.2000]
- Merkblatt 4: „Beurteilung und Behandlung der Oberflächen von Calciumsulfat-Fliessestrichen“ [IGE/WTM, VI.2000]
- Merkblatt 5: „Fugen in Calciumsulfat-Fliessestrichen“ [IGE/WTM, II.2000]
- Merkblatt : „Keramische Fliesen und Platten, Naturwerkstein und Betonwerkstein auf calciumsulfatgebundenen Estrichen“ [ZDB, I.2000]
- Merkblatt: „Hinweise für die Ausführung von Abdichtungen im Verbund mit Bekleidungen und Belägen aus Fliesen und Platten für den Innen- und Aussenbereich“ – ZDB, VIII.2000