Beton jest materiałem charakteryzującym się dużą wytrzymałością mechaniczną i odpornością na uszkodzenia. Jednakże błędy powstałe na etapie projektowania, wykonywania i wbudowywania masy betonowej oraz długotrwałe oddziaływanie szkodliwych czynników znajdujących się w powietrzu, wodzie, wpływ wilgoci, karbonatyzacja, krystalizacja soli, cykle zamarzania-odmarzania, korozja wkładek zbrojeniowych, przeciążenia konstrukcji, oraz inne agresywne czynniki - potrafią doprowadzić do zniszczeń struktury betonu.
Poniżej pokazano typowe uszkodzenia konstrukcji żelbetowych
Naprawa powinna być przeprowadzona specjalistycznymi materiałami, możliwie w największym zakresie kompatybilnymi z materiałem podłoża. Poza tym materiały te powinny uniemożliwiać dalszą degradację konstrukcji i chronić ją przed agresywnymi czynnikami znajdującymi się w otoczeniu konstrukcji.
Rodzaje korozji betonu podzielić można na:
- mechaniczną,
- fizyczną,
- biologiczną,
- chemiczną.
Podstawowym etapem robót naprawczych jest ocena stanu istniejącego i przyczyn uszkodzeń. Na tej podstawie określa się sposób naprawy oraz dobiera optymalne rozwiązania materiałowe.
Prace naprawcze podzielić można na:
- naprawę uszkodzonych miejsc przez uzupełnienie ubytków polimerowo- cementowymi zaprawami o wysokiej wytrzymałości (tzw. systemy PCC, aplikowane zarówno ręcznie jak i mechanicznie),
- naprawy rys i pęknięć wykonane metodą iniekcji (tzw. klejenie siłowe),
- naprawę materiałami na bazie kompozytów żywicznych,
- wykonanie kompleksowych powłok zabezpieczająco-ochronnych (np. na bazie mineralnych mikrozapraw, powłok bitumicznych lub materiałów żywicznych),
- wzmacnianie konstrukcji.
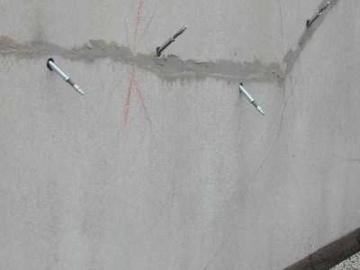
Naprawa pęknięć metodą iniekcji
W większości przypadków naprawy uszkodzeń w użytkowanych konstrukcjach żelbetowych prowadzone są w celu:
- zahamowania procesów korozji stali zbrojeniowej,
- powstrzymania postępującej degradacji konstrukcji,
- uzupełnienia ubytków w konstrukcji i odtworzenia stanu jaki występował w naprawianej konstrukcji przed jej uszkodzeniem,
- umożliwienia użytkowania konstrukcji zgodnie z jej pierwotnym przeznaczeniem.
Od zastosowanej technologii naprawy betonu wymaga się, aby zapewniała skuteczną i trwałą rekonstrukcję naprawianego materiału i późniejszą ochronę konstrukcji poprzez zapewnienie dobrej współpracy zastosowanego tworzywa i materiału istniejącej konstrukcji oraz przeciwdziałanie ponownej degradacji. Do najistotniejszych właściwości i własności materiału rekonstrukcyjnego (w porównaniu do materiału w istniejącej konstrukcji) należą:
- kompatybilność wymiarowa (skurcz, rozszerzalność cieplna, pełzanie moduł sprężystości),
- kompatybilność chemiczna,
- kompatybilność szczelnościowa,
- kompatybilność elektrochemiczna,
- utworzenie zasadowego środowiska o pH=9,5-12,5.
Zbyt duże różnice w module sprężystości mogą być przyczyną spękań lub odspojeń, brak zgodności chemicznej może wręcz powodować korozję zbrojenia (zbyt małe pH materiału renowacyjnego). Materiał wypełniający powinien chronić zarówno zbrojenie jak również zabezpieczać przed wnikaniem szkodliwych czynników z otoczenia. Istotne jest także umożliwienie dyfuzji pary wodnej (brak tej właściwości może niekiedy prowadzić do odspojenia się warstw nałożonych w czasie naprawy), a zarazem zapewnić nieprzepuszczalność dla dwutlenku węgla (zapobiega to zjawisku karbonizacji) oraz związków siarki. Stan konstrukcji można ocenić m.in. na podstawie analizy miejsc występowania i szerokości rozwarcia rys, miejsc występowania ubytków, ich rodzaju i wielkości, zawilgocenia konstrukcji, badania głębokości skarbonizowania betonu. W bardziej skomplikowanych obiektach i przy znacznych zauważalnych uszkodzeniach konieczne może być wykonanie kompleksowej analizy stanu konstrukcji.
Przy doborze materiałów naprawczych należy także uwzględnić warunki użytkowania konstrukcji:
- warunki termiczne,
- warunki wilgotnościowe,
- oddziaływanie chemiczne,
- rodzaj obciążeń oddziaływujących na konstrukcję.
Systemy naprawcze PCC zostały sklasyfikowane jako systemy typu:
PCC I - do stosowania na powierzchniach obciążonych dynamicznie oraz obciążonych ruchem kołowym,
PCC II - do stosowania na powierzchniach obciążonych dynamicznie (bez ruchu kołowego),
PCC III - do stosowania na powierzchniach nie obciążonych dynamicznie.
Zaprawy wchodzące w skład systemów są modyfikowane polimerami, które zapewniają:
- zredukowanie ilości wody zarobowej - dają to zaprawy o dobrej urabialności i małym skurczu przy niskim stosunku woda/cement,
- pasywację powierzchni zbrojenia,
- polepszenie przyczepności zaprawy do betonu naprawianego,
- zwiększenie szczelności warstwy naprawianej dla wody, dwutlenku węgla, jonów chlorkowych,
- ułatwioną pielęgnację powłoki,
- wzrost wytrzymałości zaprawy na rozciąganie i zginanie.
Naprawa wymaga przestrzegania ścisłego reżimu technologicznego. Pominięcie jakiejkolwiek czynności może spowodować nieskuteczność naprawy i konieczność ponownego jej wykonania. Warunkiem niezbędnym jest tu odpowiednie przygotowanie podłoża. Musi nim być "zdrowy" beton, z czego wynika konieczność usunięcia wszystkich luźnych i osłabionych korozją fragmentów aż do odsłonięcia nienaruszonego, nieskorodowanego i nieskarbonizowanego betonu. Najlepsze rezultaty daje tu metoda tzw. lancy wodnej usuwająca słabo związane fragmenty betonu i nie powodująca mikropęknięć w zdrowym betonie. Godne polecenia jest też piaskowanie powodujące oczyszczenie z rdzy prętów zbrojeniowych. Niezależnie od zastosowanej metody usuwania niezwiązanych cząstek betonu zawsze konieczne jest oczyszczenie z rdzy istniejącego zbrojenia.
Następnym etapem robót jest nawilżenie podłoża. Pierwsze nasycenie należy przeprowadzić kilka-kilkanaście godzin przed rozpoczęciem robót poprzez spryskiwanie powierzchni wodą aż do uzyskania pełnego nasycenia (tzw. stan matowo-wilgotny). W razie potrzeby, na krótko przed rozpoczęciem robót, zabieg należy powtórzyć (usuwając nadmiar wody np. sprężonym powietrzem).
Kolejną fazą robót jest powleczenie odkrytego zbrojenia preparatem antykorozyjnym oraz zagruntowanie całej powierzchni ubytku preparatem tworzącym tzw. warstwę sczepną. Dzięki zwiększonej ilości polimeru oraz odpowiedniemu stosowi okruchowemu tworzy ona rodzaj membrany pomiędzy starym betonem oraz materiałem, z którego została wykonana naprawa. Brak warstwy sczepnej może doprowadzić do zarysowania i naderwania warstwy renowacyjnej (np. na skutek powstawania zbyt dużych naprężeń w strefie styku na skutek różnic w zakresie odkształceń sprężystych, termicznych czy też powstałych na skutek obciążenia odrywającego). Tu uwaga: w systemach nakładanych mechanicznie warstwa sczepna nie występuje.
Ostatnim etapem jest, w zależności od charakteru usuwanych uszkodzeń nałożenie właściwej masy naprawczej oraz pomalowanie odnowionej już powierzchni elewacyjną ochronną powłoką malarską.
Pamiętać należy, że błędne określenie przyczyn korozji, stosowanie niesprawdzonych czy też przypadkowych materiałów, może przyspieszyć degradację konstrukcji, co naraża Inwestora na konieczność wykonania ponownej naprawy i znacznie zwiększa koszty całej roboty.
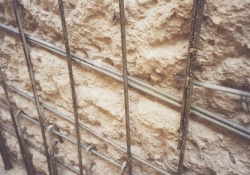 |
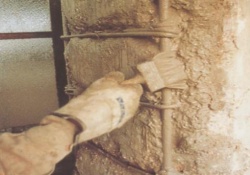 |
Odpowiednio przygotowane podłoże |
Nakładanie warstwy sczepnej |