Przedstawione w poprzednich artykułach ("Kostka została rzucona" BzG 2/2014 i "Nawierzchnie monolityczne" BzG 3/2014) różne rodzaje materiałów (naturalne, sztuczne), technologie ich wbudowywania i tym samym otrzymywania różnorodnych nawierzchni nie wyczerpują wszystkich możliwości, jakie jesteśmy w stanie osiągnąć. W szeroko pojętym drogownictwie, tym na mniejsze oraz tym na większe powierzchnie, cały czas trwa walka o to, kto przekona do swoich materiałów/ technologii potencjalnego inwestora (czytaj: zarobi). Można śmiało rzec, że laboratoria bez wytchnienia pracują nad otrzymaniem nowych, lepszych materiałów i technologii wytwarzania/ układania nawierzchni drogowych. Niektóre technologie znane w Europie Zachodniej i na kontynencie północnoamerykańskim od dziesięcioleci, dopiero od niedawna pojawiły się u nas. Sprawdzone w tamtych warunkach, wkraczają na polski rynek, aby co nieco uszczknąć dla siebie.
Ciekawym rozwiązaniem na budowę dróg lokalnych, gminnych, przemysłowych, placów postojowych i parkingów jest technologia betonu wałowanego (ang. RCC - Roller Compacted Concrete). Przede wszystkim, technologia ta jako bardziej ekonomiczna i trwalsza ma być alternatywnym rozwiązaniem w stosunku do nawierzchni dróg gruntowych, nawierzchni z płyt betonowych prefabrykowanych, słabych nawierzchni asfaltowych dróg lokalnych, czy też nawierzchni z kostki brukowej betonowej. Technologia RCC łączy zalety nawierzchni dróg betonowych (takich jak: trwałość, odporność na koleinowanie, niskie koszty eksploatacyjne) z szybkością układania i krótkim czasem oddania do użytkowania - typowym dla nawierzchni asfaltowych. Już po 48 godzinach od położenia nawierzchni betonowej jest ona udostępniana do ruchu drogowego, a dla pieszego niemalże "od ręki". Dzięki zastosowaniu rozkładarek do asfaltu, ten typ nawierzchni mogą wykonywać firmy specjalizujące się dotychczas w układaniu asfaltu.
Beton wałowany w odróżnieniu od klasycznego betonu lanego (PCC) nie wymaga stosowania deskowania krawędzi nawierzchni. Aby taką nawierzchnię do wbudowania otrzymać, niezbędna jest mieszanka betonowa o małej zawartości wody zarobowej. Jest to konieczne ze względu na zagęszczanie nawierzchni betonowej za pomocą walca drogowego. Zbyt mała zawartość wody powoduje, że mieszanka nie zostanie prawidłowo zagęszczona, a zbyt duża wprowadzi nierówności poprzez nadmierne zagłębianie się walca w mieszance betonowej. Stąd stosuje się mieszanki o konsystencji wilgotnej z optymalną zawartością wody, o wskaźniku wodno-cementowym od 0,30 do 0,45; typowa zawartość wody w betonie wałowanym waha się od 90 kg/m3 do 120 kg/m3. Ten bardzo niski wskaźnik wodno-cementowy, jaki uzyskują mieszanki betonu wałowanego, oraz technologia jego zagęszczania powodują zwiększenie mrozoodporności betonu (otrzymujemy niemalże beton całkowicie szczelny).
Do produkcji betonu wałowanego używa się kruszyw o maksymalnym wymiarze ziaren do 25 mm dla kruszyw łamanych i do 19 mm dla kruszywa naturalnego. Ma to zapobiec segregacji mieszanki przy transporcie i wbudowywaniu, jak również zapewnić równą i gładką powierzchnię budowanej nawierzchni drogi. W odróżnieniu od tradycyjnego betonu, w którym stosuje się kruszywo płukane oraz unika się frakcji pylastych, w technologii RCC tych pierwszych się nie stosuje, natomiast te drugie są niezbędne ze względu na poprawę stabilności mieszanki podczas zagęszczania przez walce wibracyjne.
Podstawowym cementem do produkcji betonu wałowanego jest cement z dodatkiem popiołów lotnych. Podobnie, jak i w przypadku innych nawierzchni, tak i w przypadku technologii RCC, jej grubość powinna być odpowiednio dobrana do natężenia ruchu. Nawierzchnie o grubości od 20 do 33 cm (o największej wytrzymałości) mają zastosowanie przy ruchu ciężkich pojazdów - drogi zbiorcze, przemysłowe (ruch ciężarówek i autobusów). Nawierzchnie o grubości od 15 do 23 cm znajdują zastosowanie przy budowie dróg dla lekkich i średnich ciężarówek (drogi lokalne, parkingi). Drogi osiedlowe, o małym natężeniu ruchu - dla samochodów osobowych - wymagają nawierzchni o małej wytrzymałości, wystarczy grubość 10–15 cm.
W porównaniu z tradycyjną budową nawierzchni z "betonu lanego" nawierzchnia z betonu wałowanego ze względu na niższą zawartość cementu potrzebnego do produkcji betonu, jak również bardziej efektywne i mniej pracochłonne wykonawstwo samej nawierzchni jest tańsza w budowie.
Co ciekawe, technologia betonu wałowanego jest z powodzeniem stosowana przy budowie zapór wodnych (ponad 500). Najwyższa zapora Longtan w Chinach ma 216,5 m wysokości i prawie 850 m długości. Całkowita objętość betonowej zapory wynosi 6,6 mln m3, z czego 69% to beton wałowany.
Kontynuując temat betonu, któż z nas, zwłaszcza tych proekologicznie nastawionych, nie chciałby, aby problem zanieczyszczenia środowiska zniknął, albo chociażby został mocno ograniczony? I jeszcze – aby technologia nie było kosmicznie droga - pewnie, że każdy by tak chciał. A czy tak się da i co ma z tym wszystkim wspólnego beton? Może nie do końca beton, a wchodzący w jego skład cement - cement o specjalnych właściwościach, które otrzymuje się poprzez dodatnie do niego dwutlenku tytanu (TiO2). W ten sposób otrzymujemy cement fotokatalityczny.
TiO2 to fotokatalizator charakteryzujący się wysoką absorpcją w zakresie promieniowania UV, a fotokataliza to termin oznaczający zjawisko przyśpieszenia reakcji chemicznej pod wpływem światła. Materiały zawierające TiO2 są zdolne do zredukowania niektórych zanieczyszczeń organicznych i nieorganicznych. Jakie substancje mogą ulegać degradacji pod wpływem fotokatalizy? Są to przede wszystkim tlenki azotu (NOx), tlenki siarki (SOx), tlenek węgla (CO), ozon (O3), amoniak (NH3), siarkowodór (H2S), węglowodory wielochlorowcowe, dioksyny, chlorobenzen, chlorofenol, węglowodory, węglowodory aromatyczne (benzen, fenol, toluen, etylobenzen, o-ksylen), pestycydy (Tradimefon, Primicarb, Asulam, Diazinon, MPMC, atrazyny), jak również bakterie, wirusy i grzyby. Przy tym dwutlenek tytanu nie jest ani toksyczny, ani niebezpieczny, nie zużywa się. Stąd proces fotokatalizy zachodzących reakcji chemicznych jest procesem długotrwałym i stale odnawialnym. Materiały lub produkty, w których stosowany jest cement z dwutlenkiem tytanu, są zdolne do zmniejszania stężenia szkodliwych substancji w powietrzu oraz do zachowania pierwotnej estetyki tych wyrobów przez długi czas.
Przy użyciu cementu z dodatkiem TiO2 otrzymujemy tzw. beton samoczyszczący, który ułatwia usuwanie zabrudzeń organicznych, gromadzących się na powierzchni betonowej. Samooczyszczanie jest związane z działaniem aktywowanego promieniowaniem UV dwutlenku tytanu TiO2, w efekcie którego zabrudzenia organiczne ulegają utlenianiu. Dodatkowo, powierzchnia betonowa zostaje pokryta cienkim filmem wodnym, tworzącym płaszczyznę poślizgu, co zapobiega nawarstwianiu się zanieczyszczeń. To z kolei umożliwia ich łatwe usuwanie podczas zraszania betonu wodą, np. podczas opadów deszczu. Dlatego beton ten został wykorzystany do produkcji kostki brukowej, w wykonawstwie nawierzchni drogowych, produkcji drogowych barier bezpieczeństwa, produkcji tynków i farb cementowych, dachówek cementowych itp.
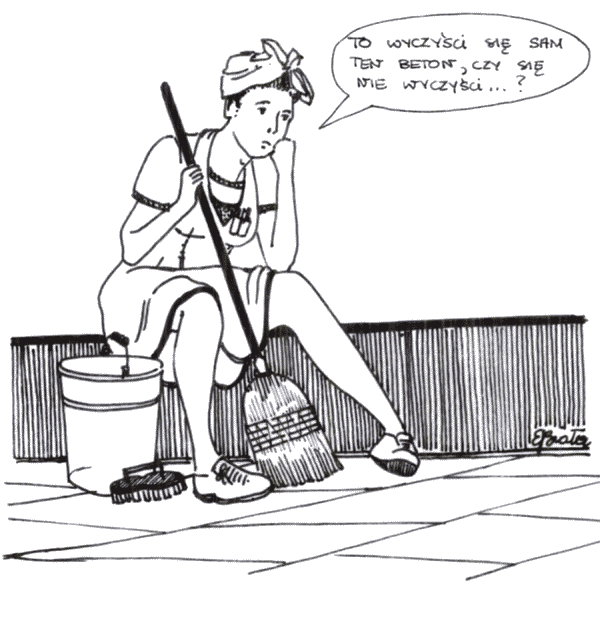
Technologia i wykorzystanie cementu z dwutlenkiem tytanu znajduje szczególne zastosowanie w produkcji wibroprasowanej kostki brukowej, tak chętnie wykorzystywanej do budowy ciągów komunikacyjnych, nawierzchni dróg, placów parkingowych. Ze względu na bezpośredni kontakt ze spalinami pochodzącymi z silników pojazdów, nawierzchnie z takiej kostki brukowej pozwalają na redukcję zanieczyszczeń w miejscu ich powstawania. Niewątpliwie uzyskujemy też lepsze walory estetyczne nawierzchni, na której ograniczony zostaje rozwój grzybów, porostów, tak często goszczących na zwykłej kostce. Przygotowanie mieszanki, formowanie kostki jest prowadzone na tych samych urządzeniach dozujących, mieszających i zagęszczających. Również czynności technologiczne związane z dojrzewaniem i składowaniem gotowych elementów są identyczne. Ponieważ aktywność fotokatalityczna wymaga dostępu promieniowania słonecznego, stąd kostka powstająca w tej technologii jest najczęściej kostką dwuwarstwową - z cienką kilkumilimetrową warstwą "aktywną". Wpływa to oczywiście na koszt samej kostki, który jest wyższy o około 15 do 20 procent w stosunku do kostki tradycyjnej.
Cement z dodatkiem TiO2 jest produkowany w dwóch klasach wytrzymałościowych 42,5R (cement szary i biały) i 52,5R (cement biały). Stąd efektywne barwienie betonu i łatwość uzyskania intensywnych kolorów kostki - efekt białej barwy dwutlenku tytanu TiO2 (biel tytanowa). Oprócz właściwości fotokatalitycznych kostka brukowa z wykorzystaniem cementu z TiO2 charakteryzuje się również wysokimi parametrami technicznymi: wysoką wytrzymałością, niską nasiąkliwością oraz wysoką mrozoodpornością (efekt doszczelnionej struktury przez nanocząsteczkowy TiO2). W ten sposób otrzymaliśmy nowoczesny materiał budowlany o wysokich walorach ekologicznych, trwałościowych i estetycznych.
Jak widzimy beton sprawdza się i atakuje, choć jego największy rywal - asfalt nie pozostaje w tyle. W ostatnim czasie można było przeczytać o innowacyjnej technologii nawierzchni długowiecznych z asfaltu. Tak, właśnie z asfaltu, którego do tej pory jedną z największych wad była jego "krótkowieczność". Przyjrzyjmy się zatem technologii asfaltu.
Przy budowie dróg w Polsce będzie można zastosować technologię, która jest innowacyjna nie tylko w naszym kraju, ale również na skalę europejską. Co bardzo ważne, zwłaszcza na naszym rodzimym (połatanym) podwórku zwiększy się wytrzymałość nawierzchni asfaltowych (z 20 do nawet 50 lat), a co za tym idzie - oczywiście zmniejszą się wydatki na remonty - i dalej - zmniejszą się koszty społeczne.
Technologia ta przewiduje zastosowanie w dolnej warstwie tworzonych konstrukcji specjalnego asfaltu o zwiększonej elastyczności, odporności na zmęczenie i starzenie. Takie wykorzystanie asfaltu na pewno nie jest bez znaczenia we wdrażaniu kolejnych innowacyjnych rozwiązań i technologii.
Dlaczego oprócz wydatków na remonty (co oczywiste) wspomniałem o znaczącym obniżeniu kosztów społecznych? To też nie jest takie dziwne. Pomyślmy o rosnącym z każdym rokiem natężeniu ruchu kołowego w Polsce oraz o wynikającym z niego coraz częstszym zamykaniem dróg (remonty, ach te niekończące się remonty…). Generuje to przecież ogromne koszty społeczne, które ponosimy my – wszyscy użytkownicy dróg. A przecież – to też wie każdy z nas – im droga jest bardziej obciążona ruchem, tym te koszty są dotkliwsze.
Nowa koncepcja dotycząca asfaltu wydłuży żywotność dróg bez konieczności przeprowadzania poważnych głębokich napraw konstrukcji. W nawierzchni tej potrzebne będzie jedynie okresowe odnawianie powierzchni związane z uszkodzeniami warstwy ścieralnej.
Tu pojawia się temat ekologii – wiadomą jest rzeczą, że obecnie zwiększa się zapotrzebowanie na produkty energooszczędne, a co za tym idzie także nawierzchnie muszą być „inteligentne”, wykorzystujące technologie oparte na materiałach z recyklingu. Oczywiście wiemy, że to nie jest tanie, dlatego w Polsce wciąż rzadkie; trzeba jednak pamiętać, że ma głębokie uzasadnienie zarówno ekonomiczne, jak i ekologiczne. Zgodnie z przysłowiem: „biednego nie stać na tanie rzeczy”, a także w chwili, gdy siatka komunikacyjna w Polsce i całej Europie intensywnie rozwija się, nie możemy pozwolić sobie na tanie rozwiązania, które okażą się tymczasowe.
A jak to wygląda w szczegółach? W przypadku budowy tradycyjnej konstrukcji nawierzchni asfaltowej, której trwałość powinna być zapewniona na 20 lat, najniższa warstwa konstrukcji asfaltowej - tzw. podbudowa - jest warstwą najgrubszą i zbudowaną z materiałów grubszych, sztywniejszych niż warstwy leżące wyżej, tj. warstwa ścieralna czy wiążąca. Jednakże to warstwa podbudowy jest decydującym elementem konstrukcji zapewniającym jej trwałość; w niej bowiem powstają największe naprężenia generowane przez pojazdy i to właśnie tam rozpoczyna się degradacja nawierzchni. W przeciwieństwie do nawierzchni tradycyjnej, projekt nawierzchni długowiecznej zakłada budowę warstwy podbudowy elastycznej, mniej sztywnej, ale wysoko odpornej na zmęczenie od cyklicznego obciążenia ruchem. Właśnie przez taką modyfikację podbudowy kilkakrotnie wzrasta trwałość całej konstrukcji. Do warstwy pośredniej, wiążącej, stosuje się zaś materiał odporny na koleinowanie: mieszanki asfaltowe z wysokim modułem sztywności, od niedawna stosowane przy budowie autostrad.
Te nowoczesne rozwiązania zakładają przede wszystkim dobór odpowiednich materiałów do właściwej nawierzchni w taki sposób, aby każda z nich w sposób optymalny spełniała swoją funkcję. I tak: przy warstwie wiążącej, która de facto pełni rolę „nośnika” konstrukcji, kładzie się nacisk na to, aby charakteryzowała się sztywnością i odpornością na spękania, szczególnie te spowodowane niskimi temperaturami. Natomiast w warstwie podbudowy (tzw. antyzmęczeniowej) zastosowanie znajduje mieszanka elastyczna i odporna na działanie powtarzających się obciążeń.
Zatem wystarczy „tylko” zebrać odpowiednie fundusze i jak najszybciej przystąpić do budowy dróg, tak aby nasz przecież piękny kraj przestał się kojarzyć z dziurawym serem, a w najlepszym razie z miejscem, w którym co krok trwa generalny remont nawierzchni…